About us
We are a leading European printed circuit board (PCB) design company, specializing in high-performance layout design for high-speed, high-density and high-power applications in consumer and industrial markets.
We provide customers with low-cost, turn-key solutions to prototyping and production-engineering challenges, that minimize design and production costs, as well as risk. We have one of the longest track records in the industry, with >35 years of activity and >12 years of UNI EN ISO9001 accreditation. We have working knowledge and experience with most European and worldwide certification requirements.
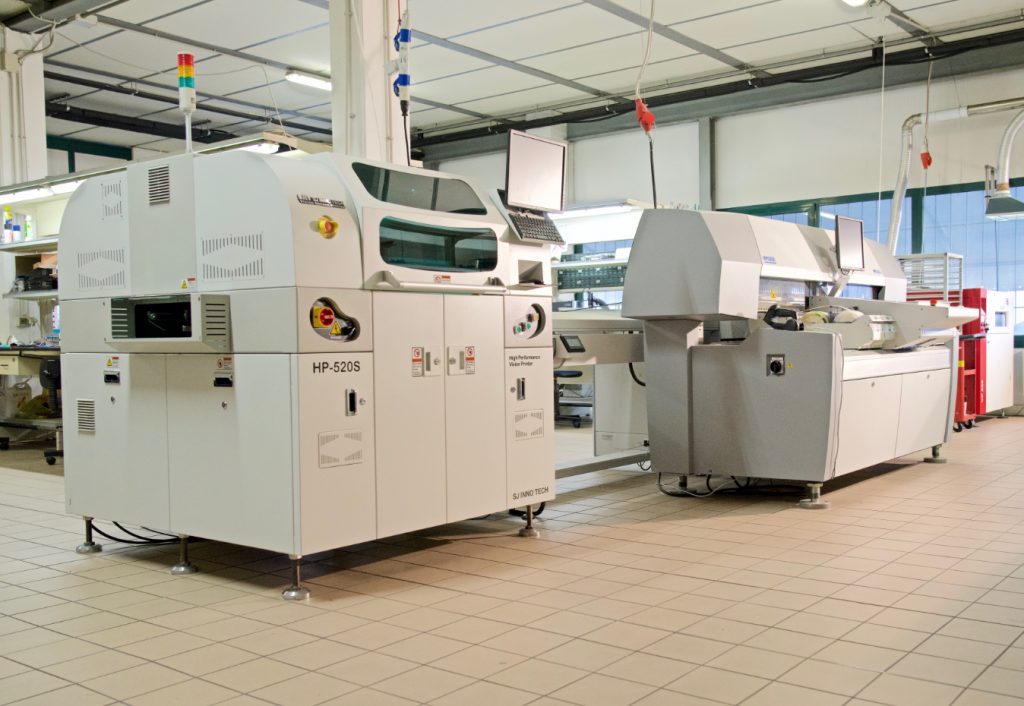
What are our capabilities?
We cater for a diverse customer base, and routinely design PCBs of varying complexity, ranging from 1 to >20 layers, using rigid as well as flexible and hybrid substrates, with through as well as buried vias. We also offer our customers complete 3D modelling solutions for space-constrained applications, and formal signal-integrity and cross-talk analysis. We can work with the Orcad, PADS and DX Designer environments, and have in-house conversion tools that enable us to read and write many other formats too. We also provide complete prototyping solutions, and can take care of component procurement, PCB assembly and prototype testing and characterization.
We invite you to view our competences related to:
Certificated quality
A constant drive towards improvement of our design and prototyping services has led to Tecno 77 being awarded the ISO 9000 certification on January 2001, in the field of Printed Circuit Board Layout.
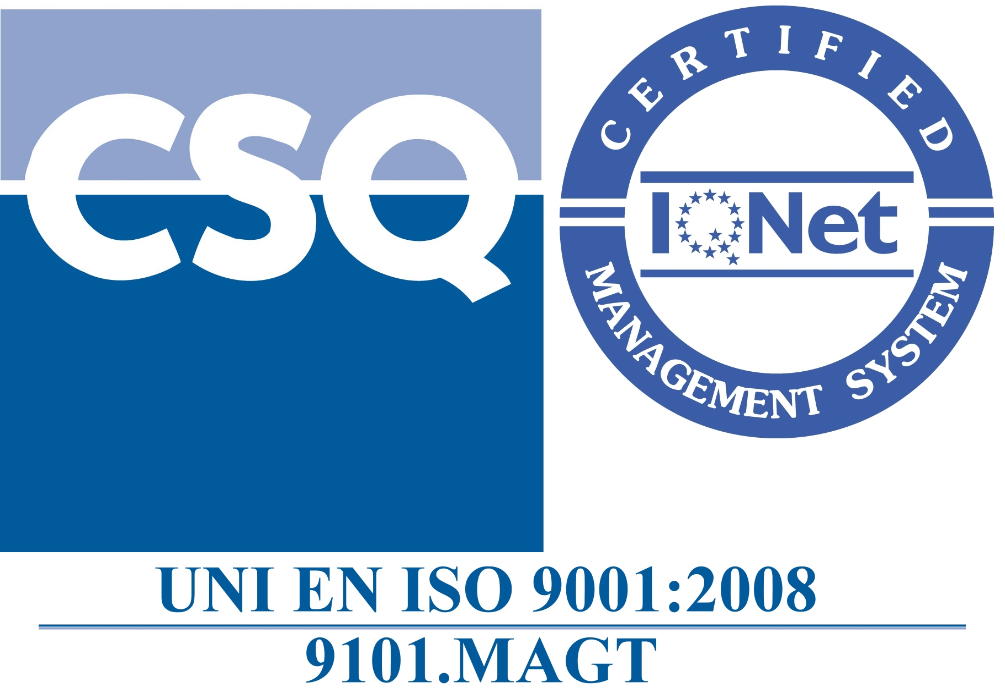
Our story
If you open any electronics equipment, you can see that all the components are mounted on a board where are drawn all the tracks to connect the components pins.
This board, to be realized, need a “Master” or Printed Circuit Board Layout.
The Printed Circuit Board Layout is composed by some sheet and afterwards by some film, where is represented the track layout, needed to carry out all the connection between the components needed to realize any electronic circuit.
Using this films, we obtained the real PCB, composed by an insulated base, “vetronite” (FR4), “bachelite” or similar, where has been glued a thin sheet of copper.
Using a photoengraving process, the unnecessary copper is eliminated and on the PCB remain all the needed tracks for the connections. Other films are needed to realize the Solder Mask that is a thin paint layer needed to protect the tracks where soldering is not needed, from oxidation and dust.
In 1977 the Personal Computer were non-existent as well as the Programs needed to realize a Printed Circuit Board Layout or "Master" so all the work to make it was hand-made.
The first Masters made by Tecno77 were made using a support called "Ulano". The Ulano is a transparent film on which was applied a thin colored layer that is removable.
First, on a sheet, you had to draw by hand the tracks layout and the components dimension, starting from the schematic layout.
The work was somewhat simplified with the advent of the Adhesive Transfer Tape and sheet of Dry-Transfer Pads.
Always usign a Reference Sheet, on which were traced the tracks taking into account the insulation and the dimensions of the components, began the task of copy using the Dry-Transfer Pads and the Adhesive Tape. On a sheet of acetate, helped by a backlighted table on wich was applied a graduated sheet, were first applied the Dry-Transfer Pads and then the connections were achieved through the application of Adhesive Tape.
Even in this case, however, the layer were to be implemented one by one.
In this period began to be available the first Home Computer made by IBM and the first programs to implement the master. The programs were very expensive and so were the first Computers, but there was a great advantage in achieving Master for Printed Circuit Board with the help of a Program on your computer.
Once completed the work, all the faces were made without having to start over again to draw the Pads for the second layer, for the Solder Mask, then the tracks etc.
At the end of the routing and verified the errors, the files generated by the program were sent to a pen plotter that printed in scale 1:1 or 2:1 the "film".
After a few years, with the advent of the photoplotter laser, was achieved a significant improvement of the work, both in terms of speed than in the accuracy.
With the photoplotter laser, in fact, were obtained directly the films used in the production process through photoengraving.
Increased complexity, speed signal, number of components and reduced physical dimensions of the components, make it impossible today the creation of master made "By-Hand", without the aid of dedicated computer programs, useful to take into account the insulation, the size and length of tracks, etc.
The work of the "Master Designer" is always a manual work, but any aid coming from dedicated programs to simplify the work itself is welcome so the Master Designer can focus more on the desired result, namely to obtain a card good and running and, why not, also "nice" to be seen aesthetically.